Business Process Modelling and Improvement
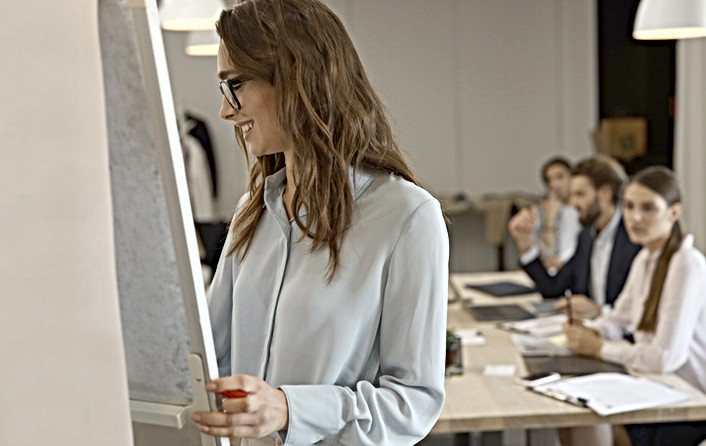

In today’s competitive environment, operational efficiency is paramount. ForJo Consulting specialises in Business Process Modelling and Improvement, helping organisations visualise and optimise their processes for enhanced performance. We believe that clear, well-defined processes are the foundation of a successful organisation.
Key Benefits
Streamlined Operations
Our approach identifies inefficiencies and redundancies, leading to streamlined processes that save time and reduce costs.
Enhanced Productivity
By optimising workflows, we empower your employees to work more effectively, leading to improved overall productivity and job satisfaction.
Increased Customer Satisfaction
Well-structured processes result in quicker response times and higher-quality outputs, enhancing your customers' overall experience.
Our Approach
1
Process Mapping
We collaborate with your team to create visual representations of your existing processes, highlighting each step and its interconnections.
2
Analysis
Utilising various analytical tools, we identify bottlenecks, redundancies, and areas ripe for improvement, focusing on both efficiency and effectiveness.
3
Implementation
Our consultants work closely with your staff to implement best practices and innovative methodologies, ensuring that the changes are sustainable and positively impact your organisation.
Why Choose Us
With a focus on collaboration and continuous improvement, we are dedicated to working alongside your team to ensure that any changes are embraced and sustained. Our commitment to operational excellence drives us to deliver measurable improvements.
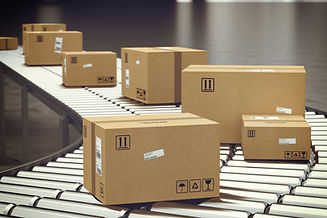
Case Study
Process Optimisation for a Logistics Company
Client
A logistics company struggling with inefficiencies in its delivery and warehousing processes.
Challenge
High operational costs, slow delivery times, and order fulfillment errors were affecting the company’s profitability and customer satisfaction.
Solution
ForJo Consulting mapped the client’s existing processes, focusing on key workflows related to order processing, inventory management, and dispatch. We identified bottlenecks, redundant steps, and gaps in resource allocation, then designed optimised workflows to eliminate inefficiencies.
Results
Operational Efficiency: By streamlining processes, the client reduced delivery times by 25% and decreased warehousing costs by 15%.
​
Increased Accuracy: Improved processes reduced order errors by 40%, leading to higher customer satisfaction.
​
Cost Savings: The client saved £200,000 annually in operational costs and reported increased employee productivity and morale.